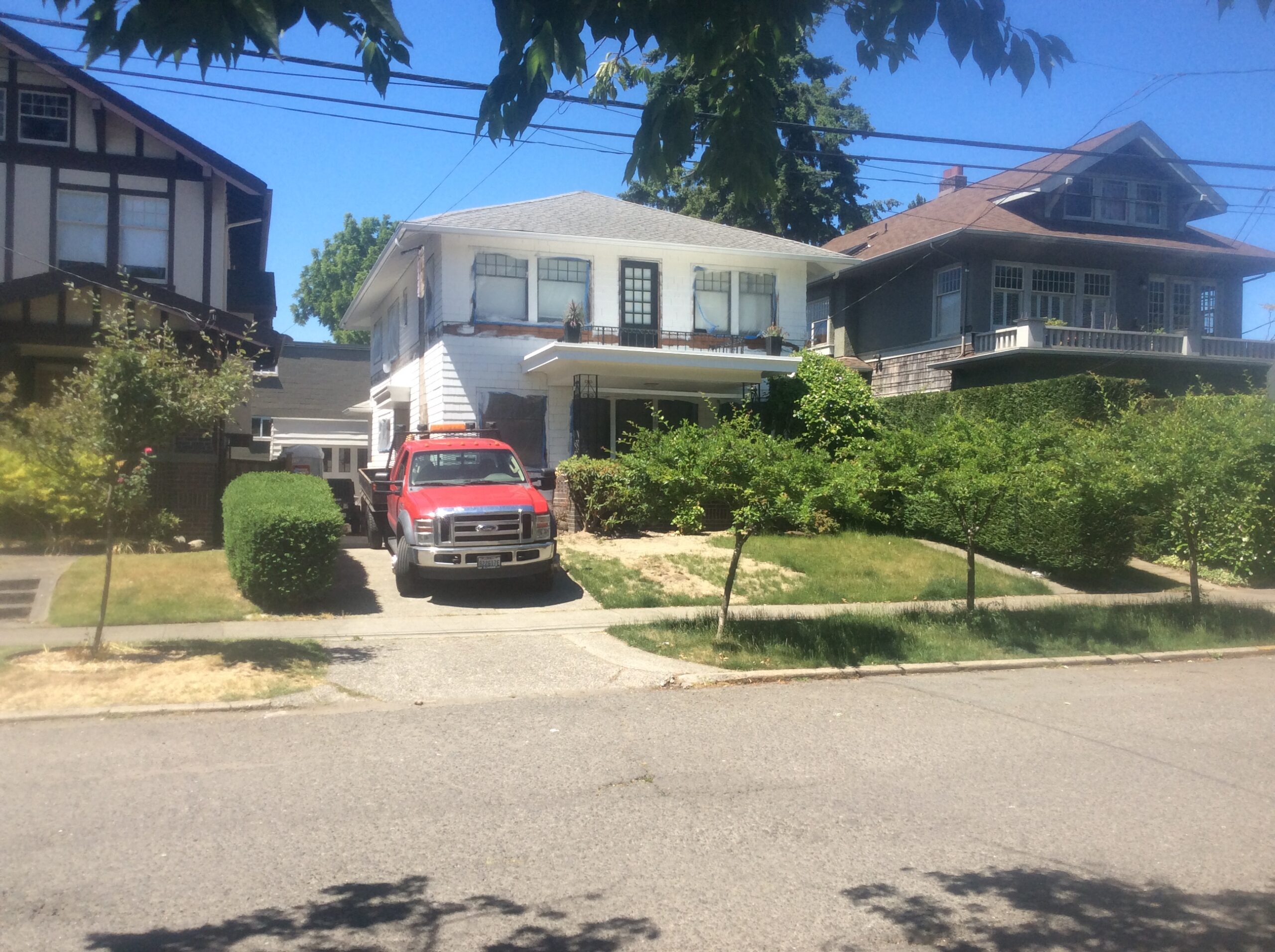
Built about 1908, this residence was built partially over a filled in pond . As a result the SE corner settled 4-5 inches early after the build. The new owners decided to repair this, but also to add 14.5 inches, 2 steps worth of rises allowing more head room in the daylight basement. In this shot the old vinyl siding is removed and a repair attempt of the cedar shingles is on going. Also the belly bands are off the house.
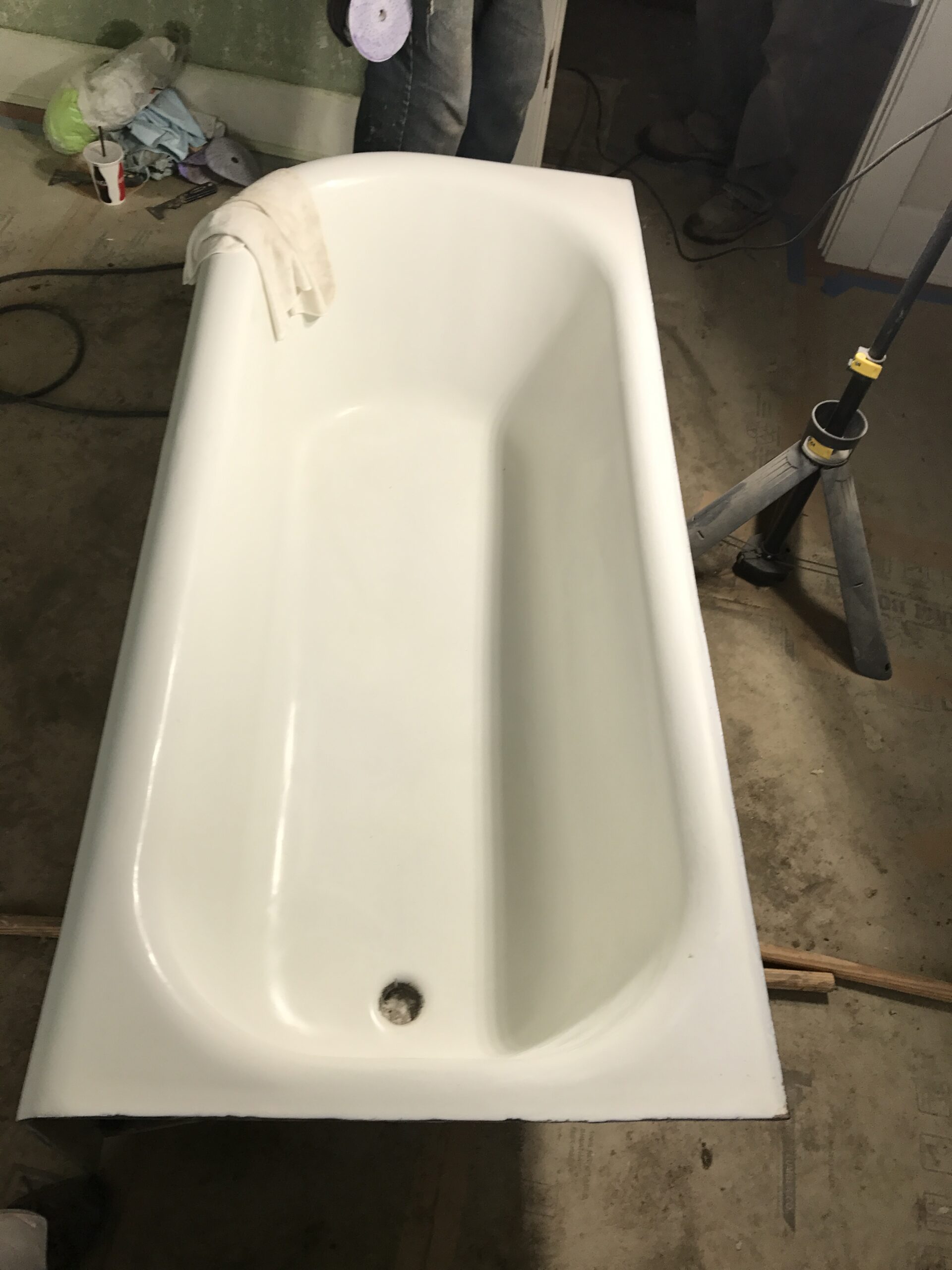
Two sided cast iron apron, repurposed from another residence, polished finish, not painted
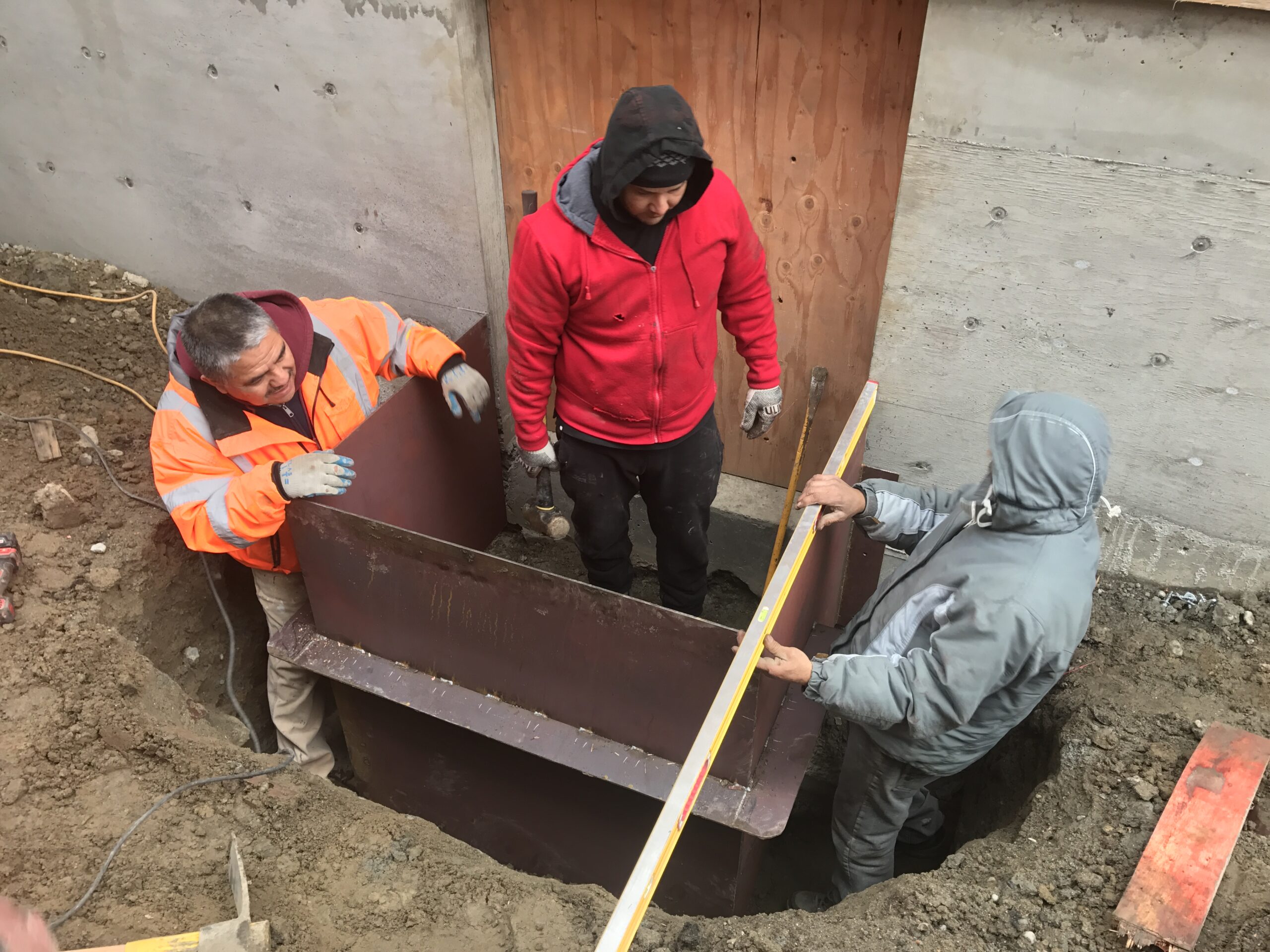
Egress window box, Corten steel
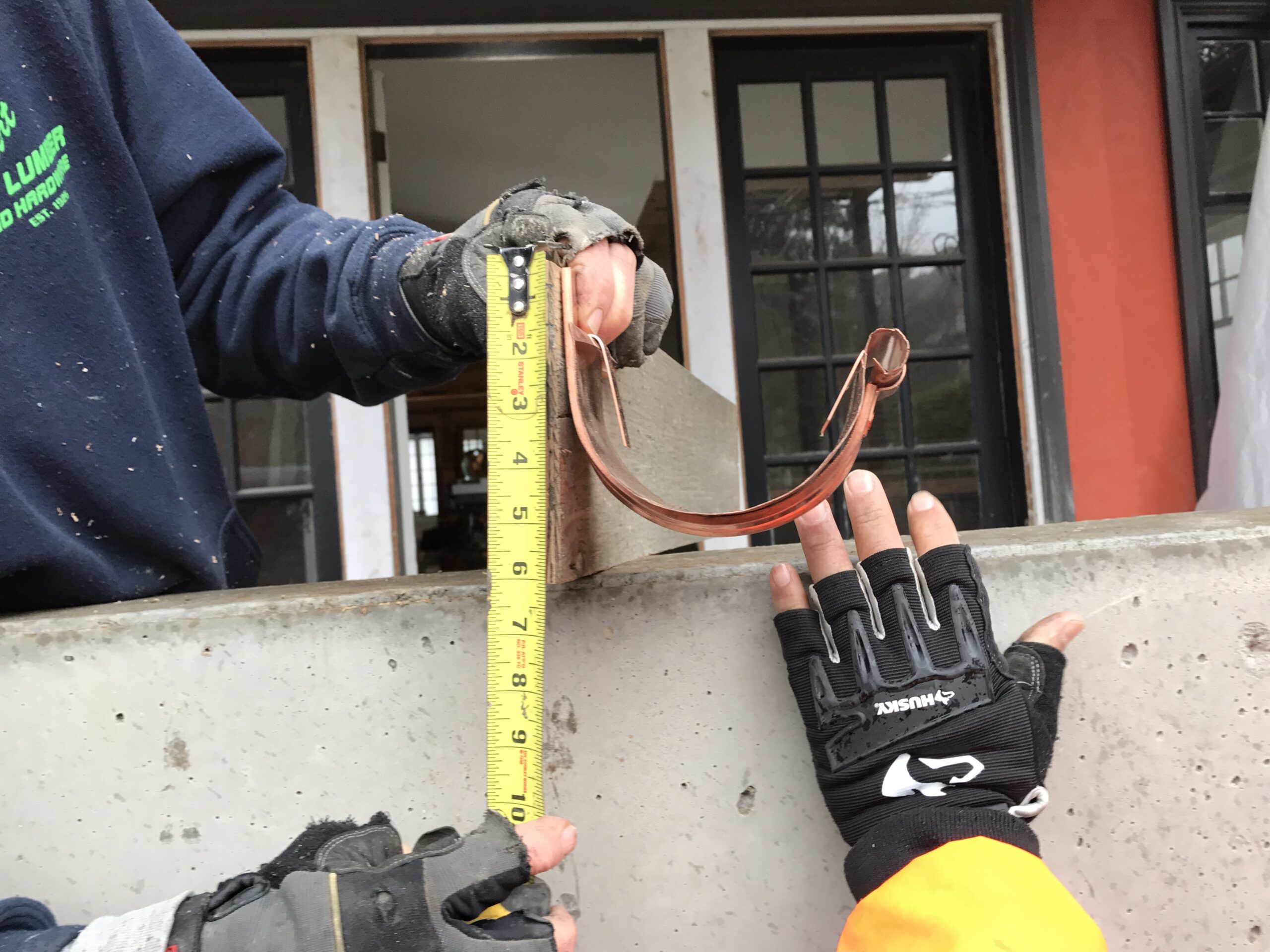
New copper gutter and down spouts, this is a bracket

Applying a sealant to the interior of the daylight basement’s walls
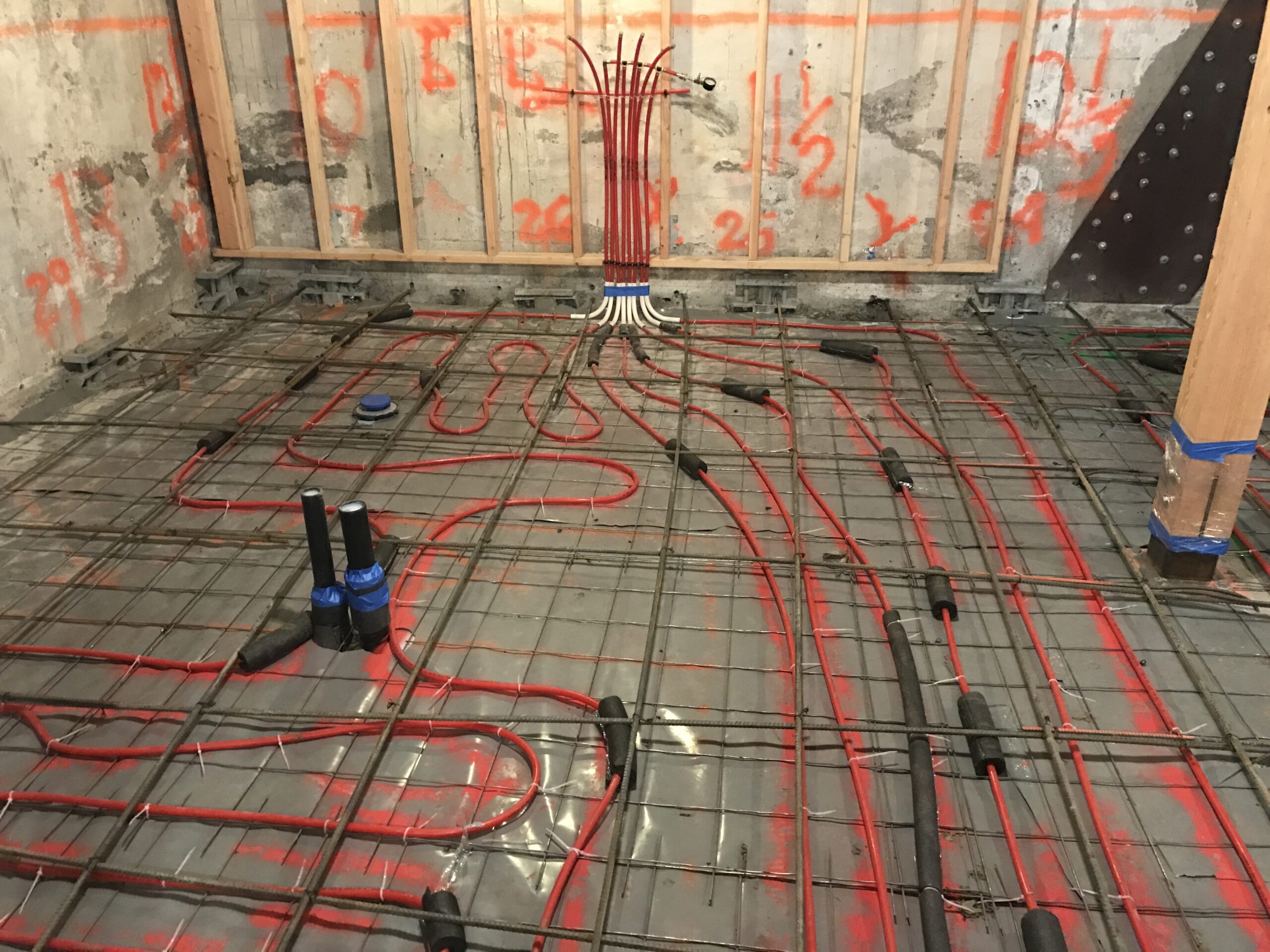
Basement hydronic heating tubing
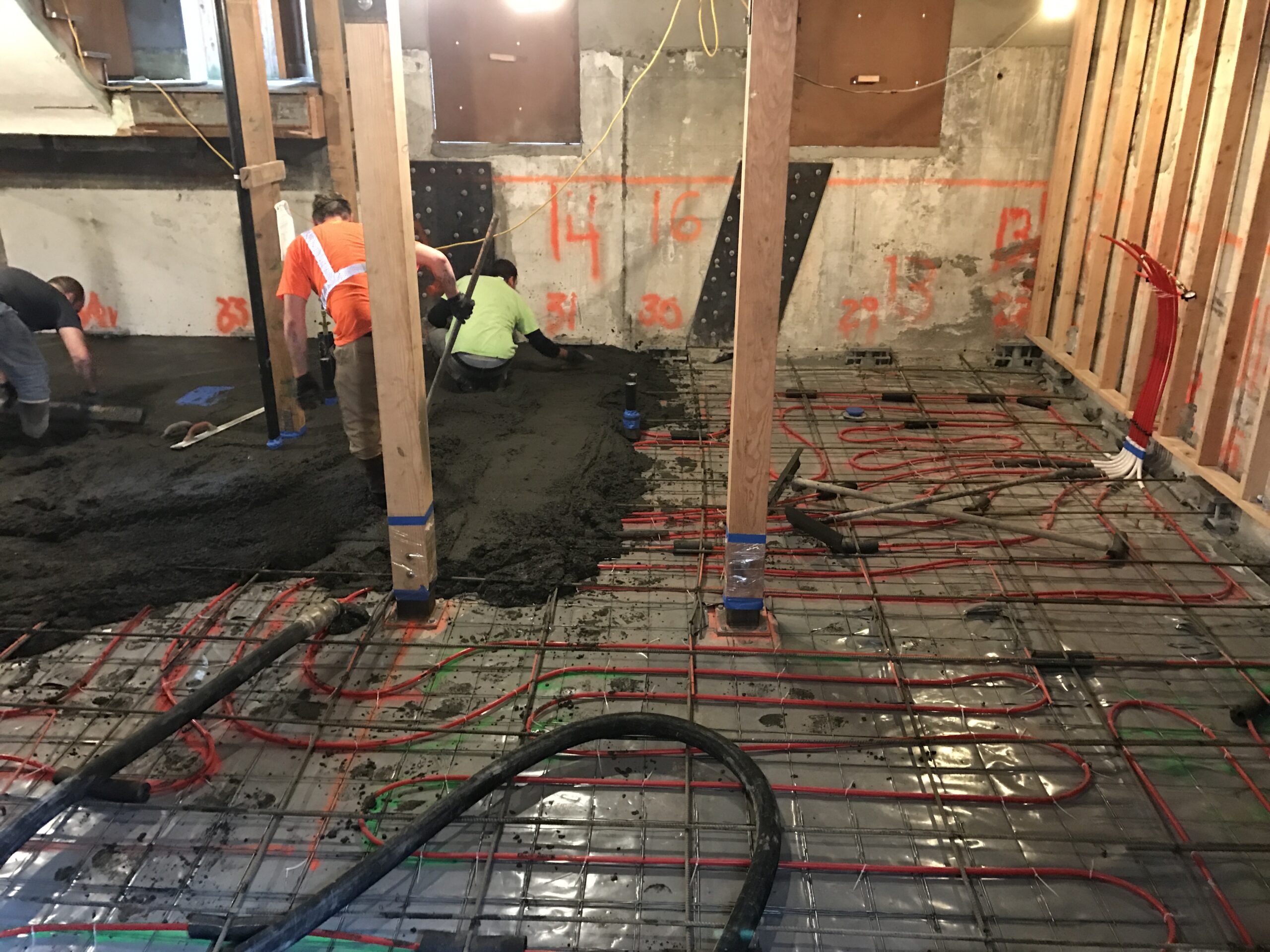
Placing concrete slab
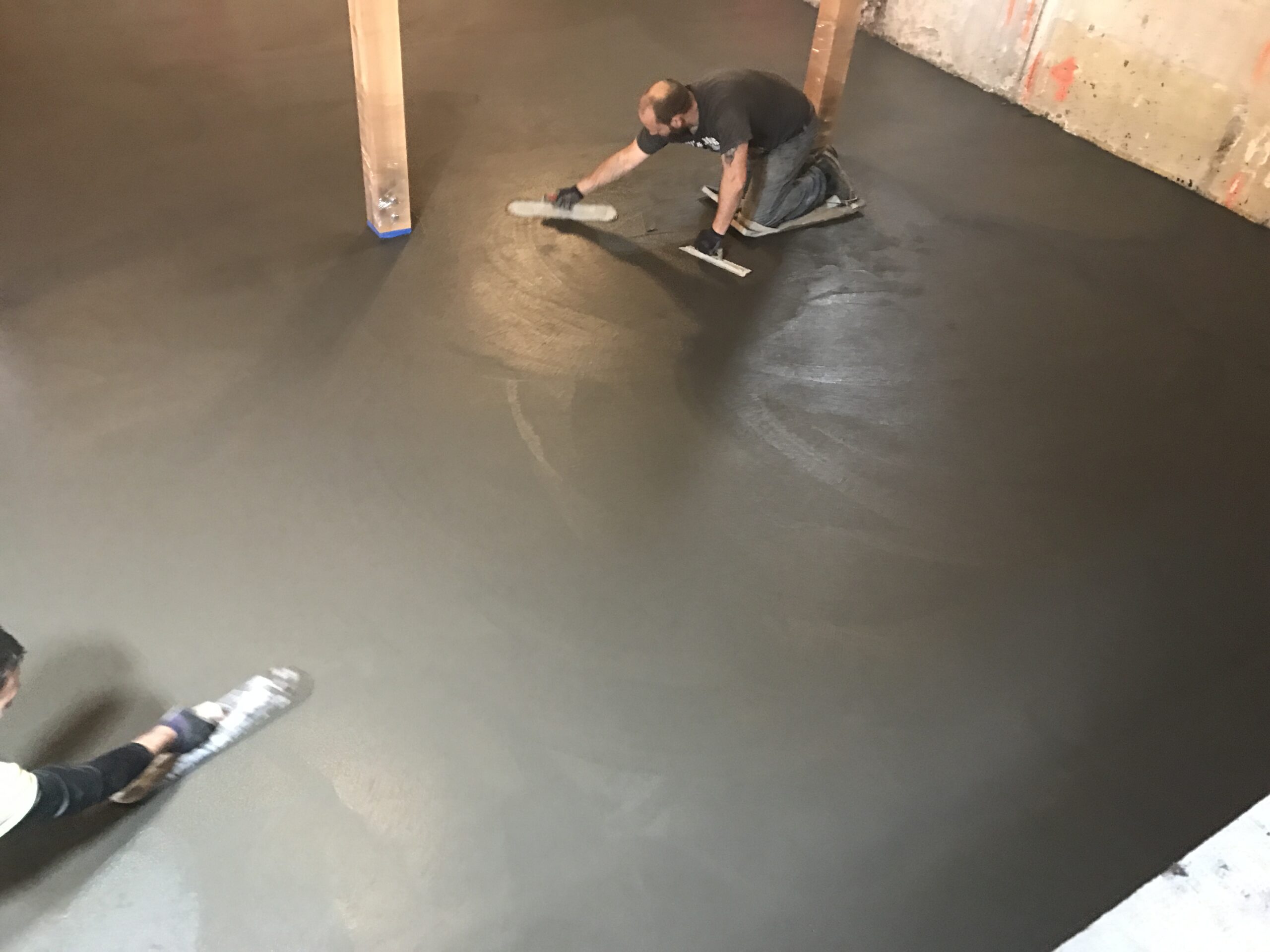
Finishing concrete slab
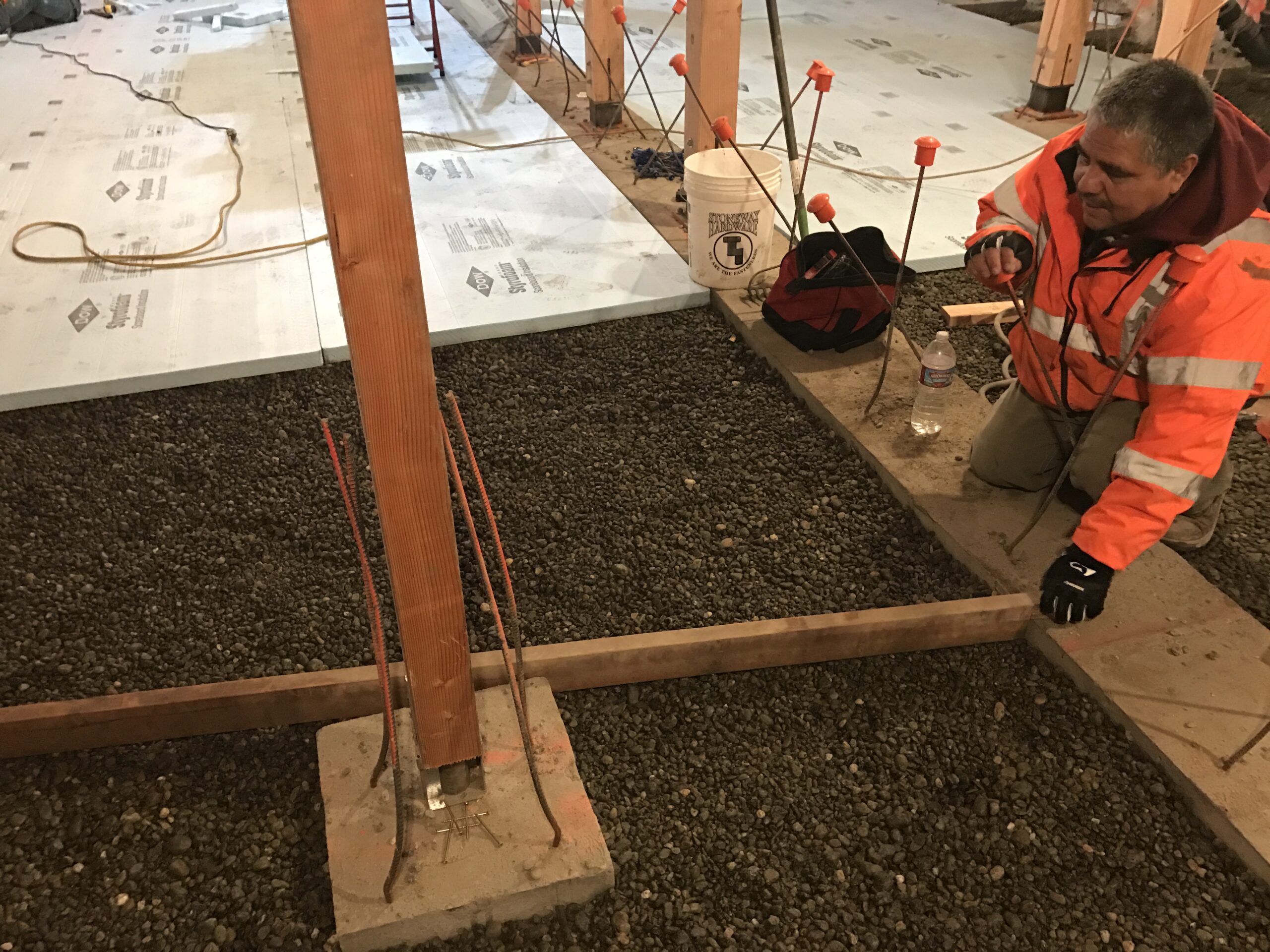
Gravel base and foam insulation being installed. This is also Miguel Rocha, he is awesome.
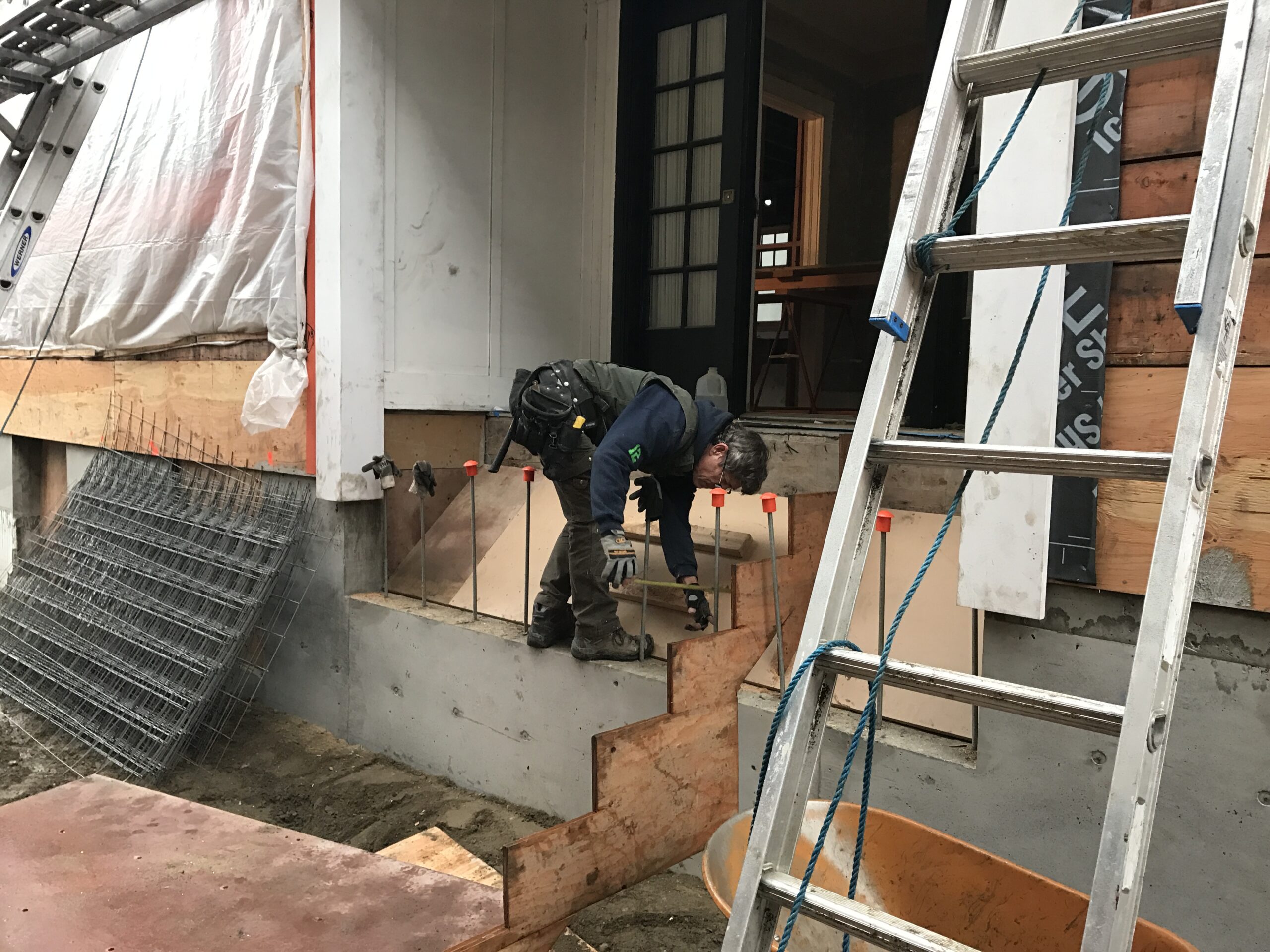
Foundation topper poured, new entry concrete stairs being started
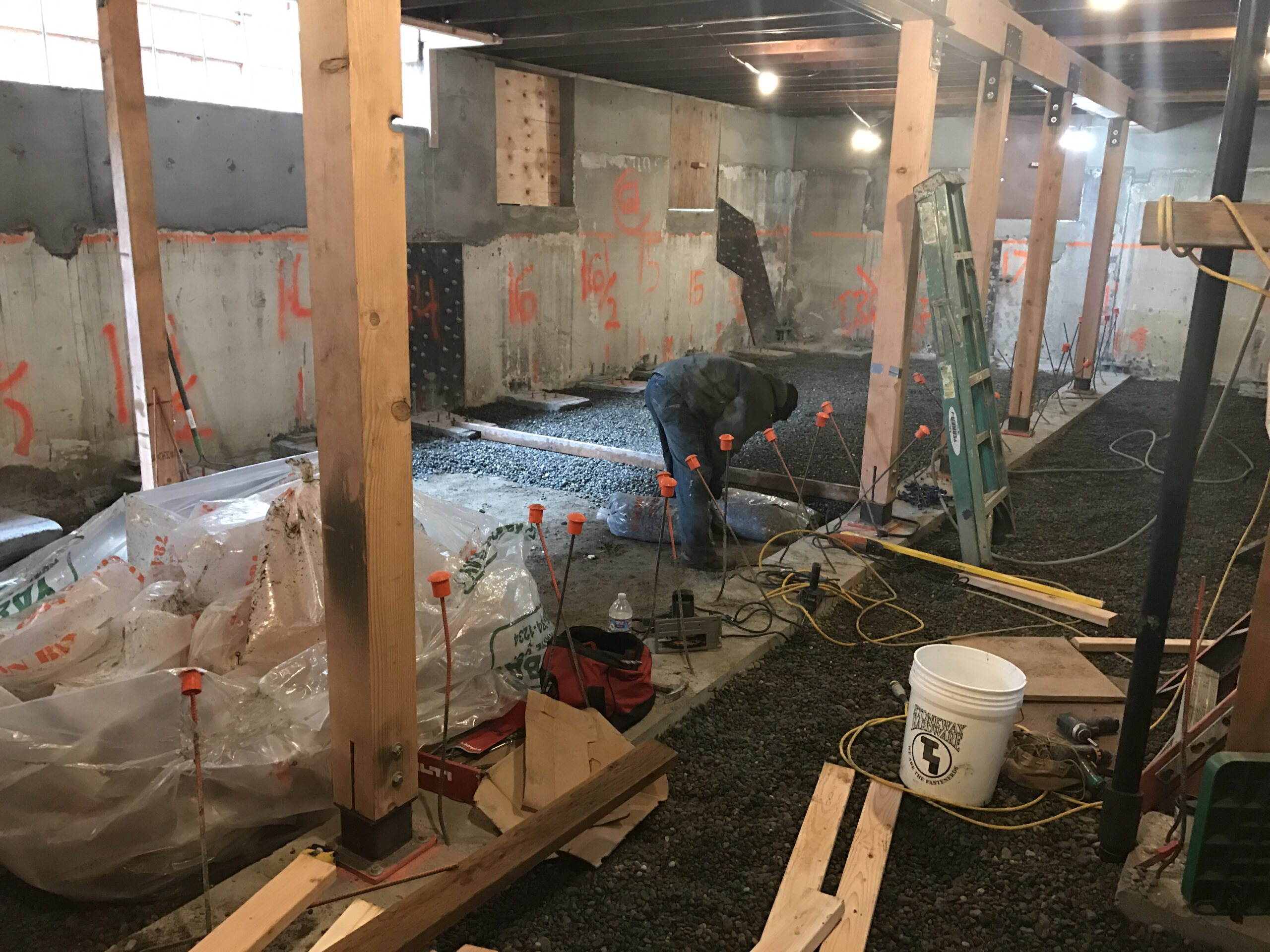
Around the walls we see the concrete captured pin pile heads , 1/2 steel plate wall reinforcing, new foundation wall topper and blockouts for new future daylight windows.All the electrical, water, sewer, and gas lines aremoved and disconnected.
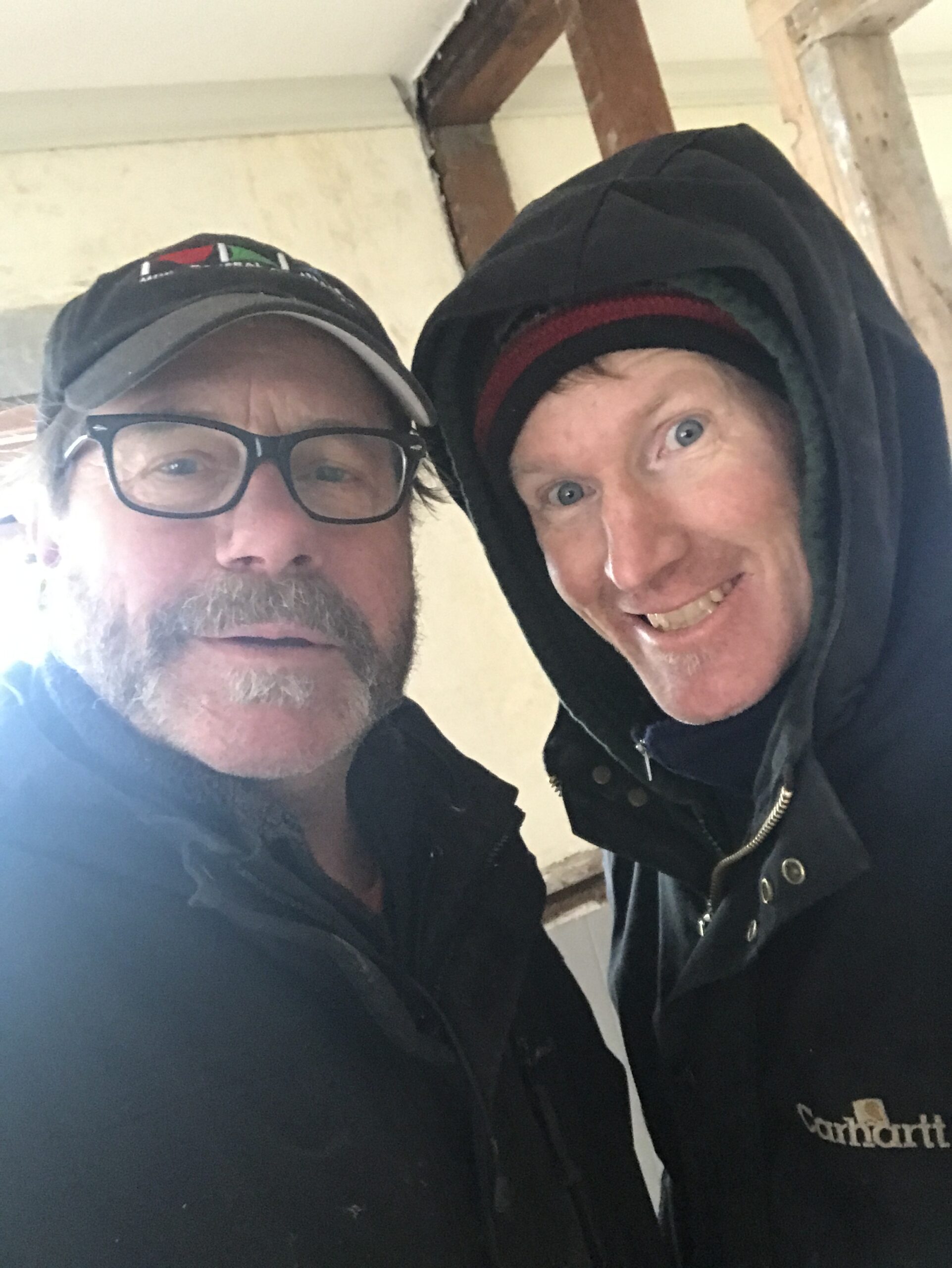
More of the excellent finish crew, thank you Eric Moultan
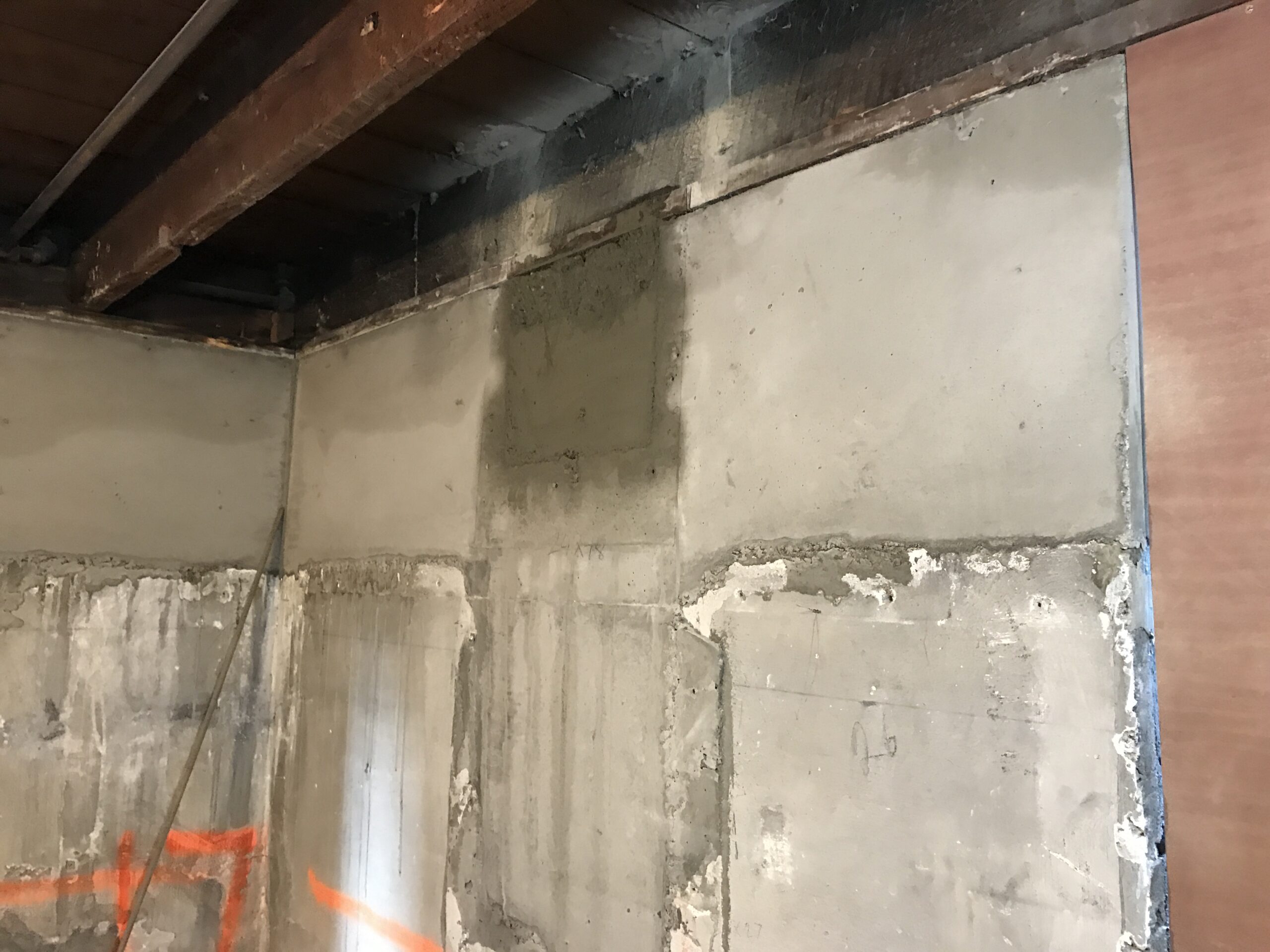
This concrete pour is where the houser lifting I beams came out after settling the house down, there are 4 of these
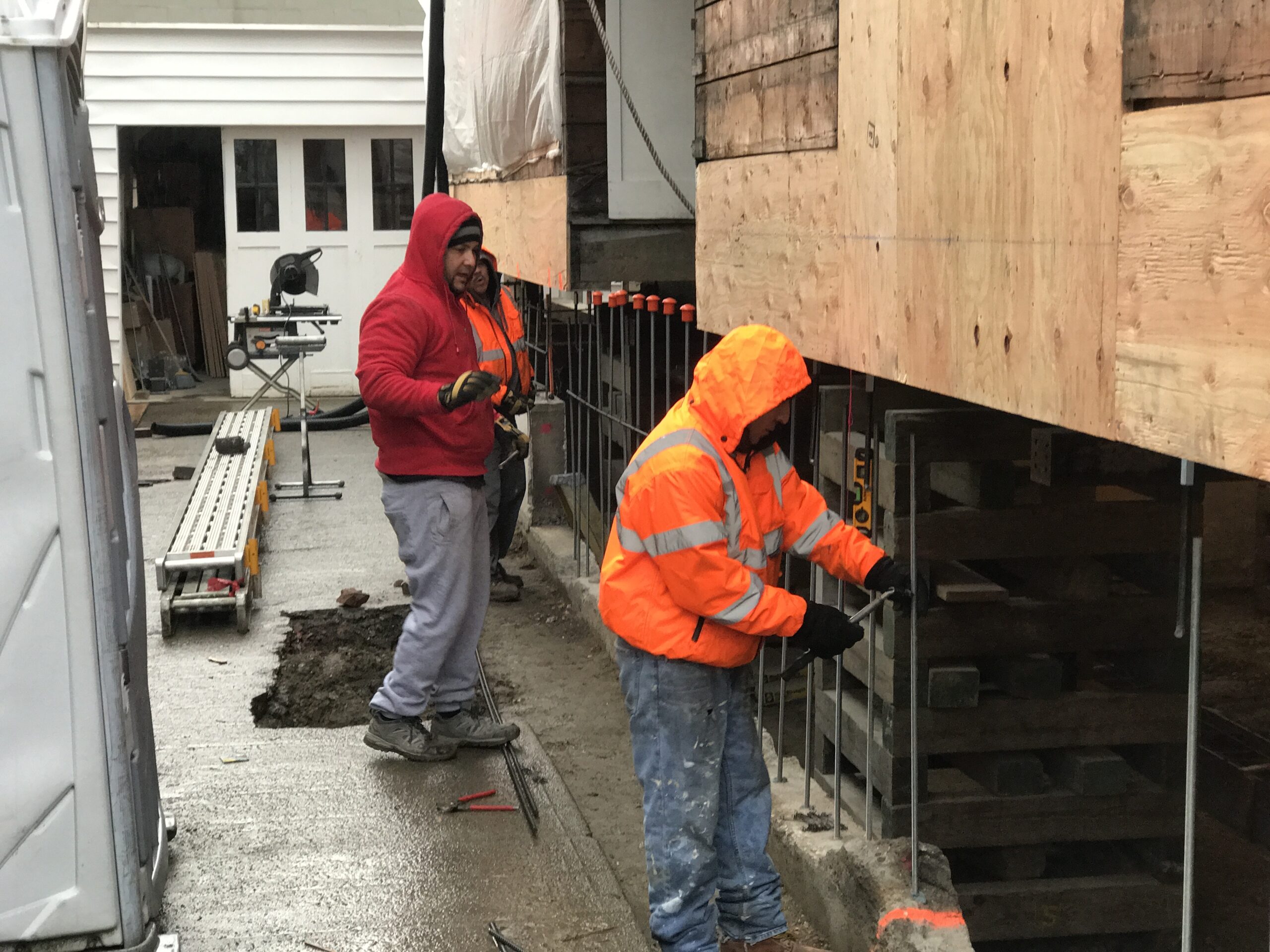
Threaded rod epoxied into the top of the existing foundation
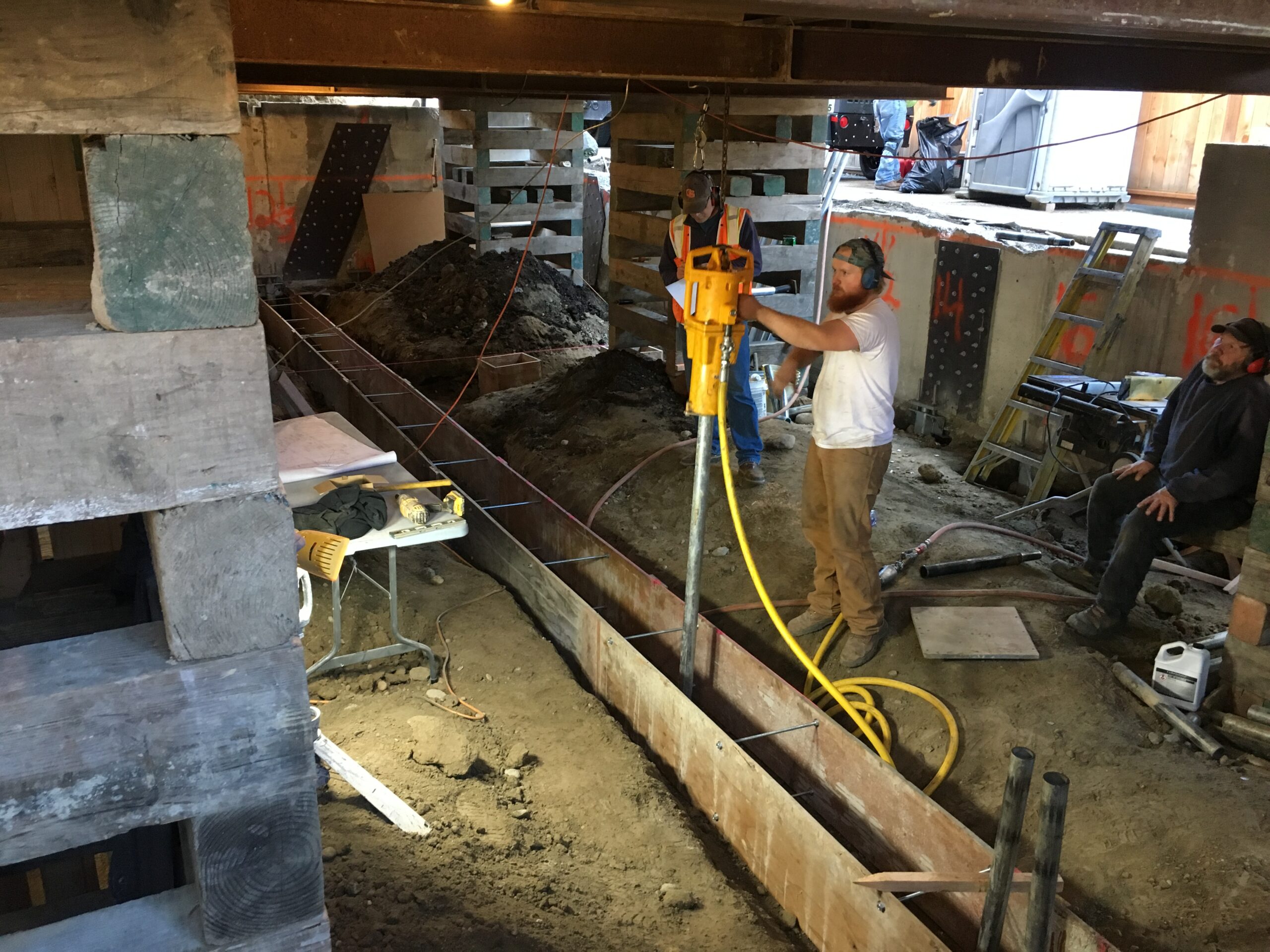
90 lb Jack hammer driving 2 inch pin piles to refusal down the new centerline footing
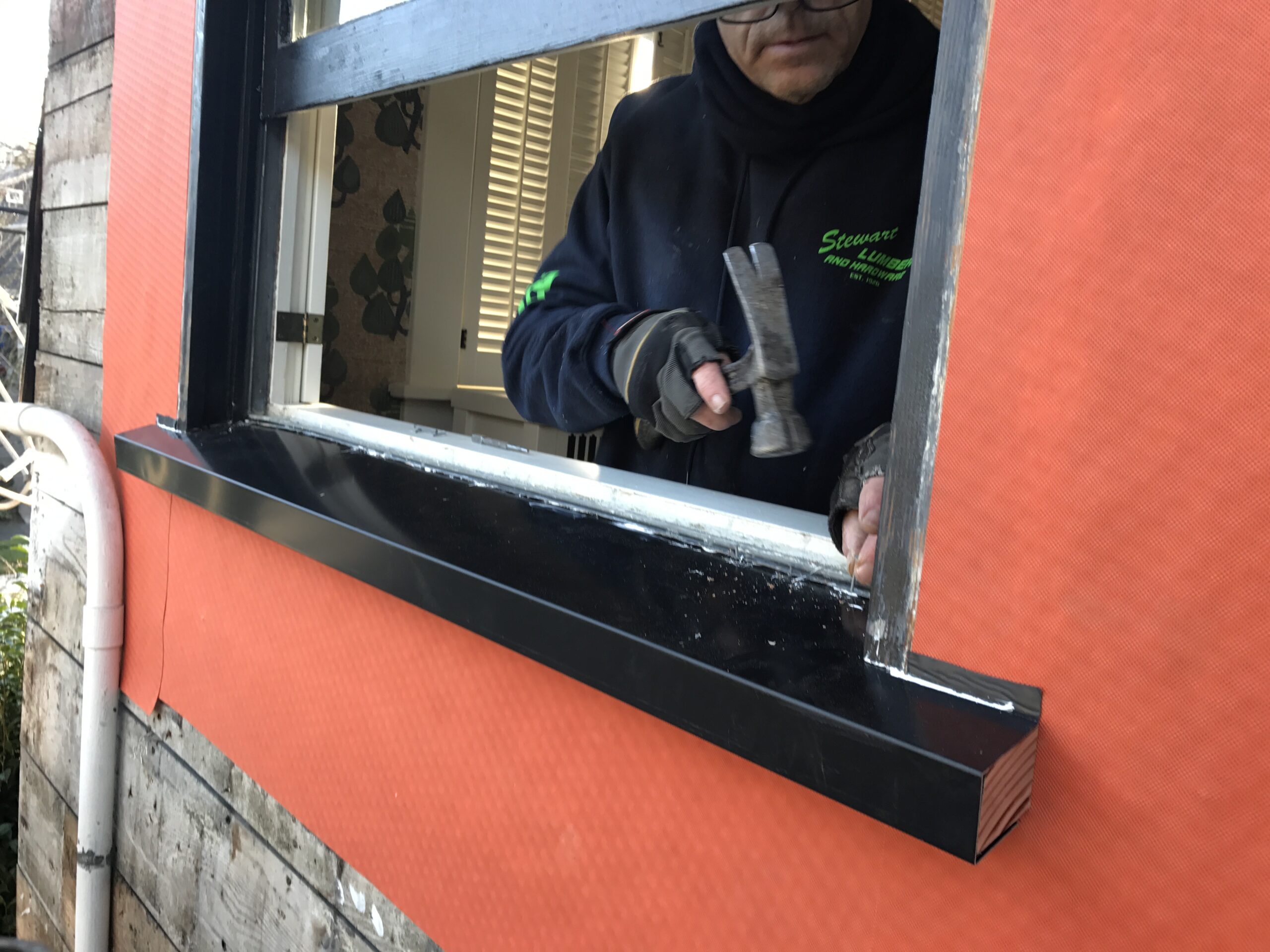
All of the window sill tails were removed for the vinyl siding, metal sill covers were fabricated allowing sill extensions to be added.
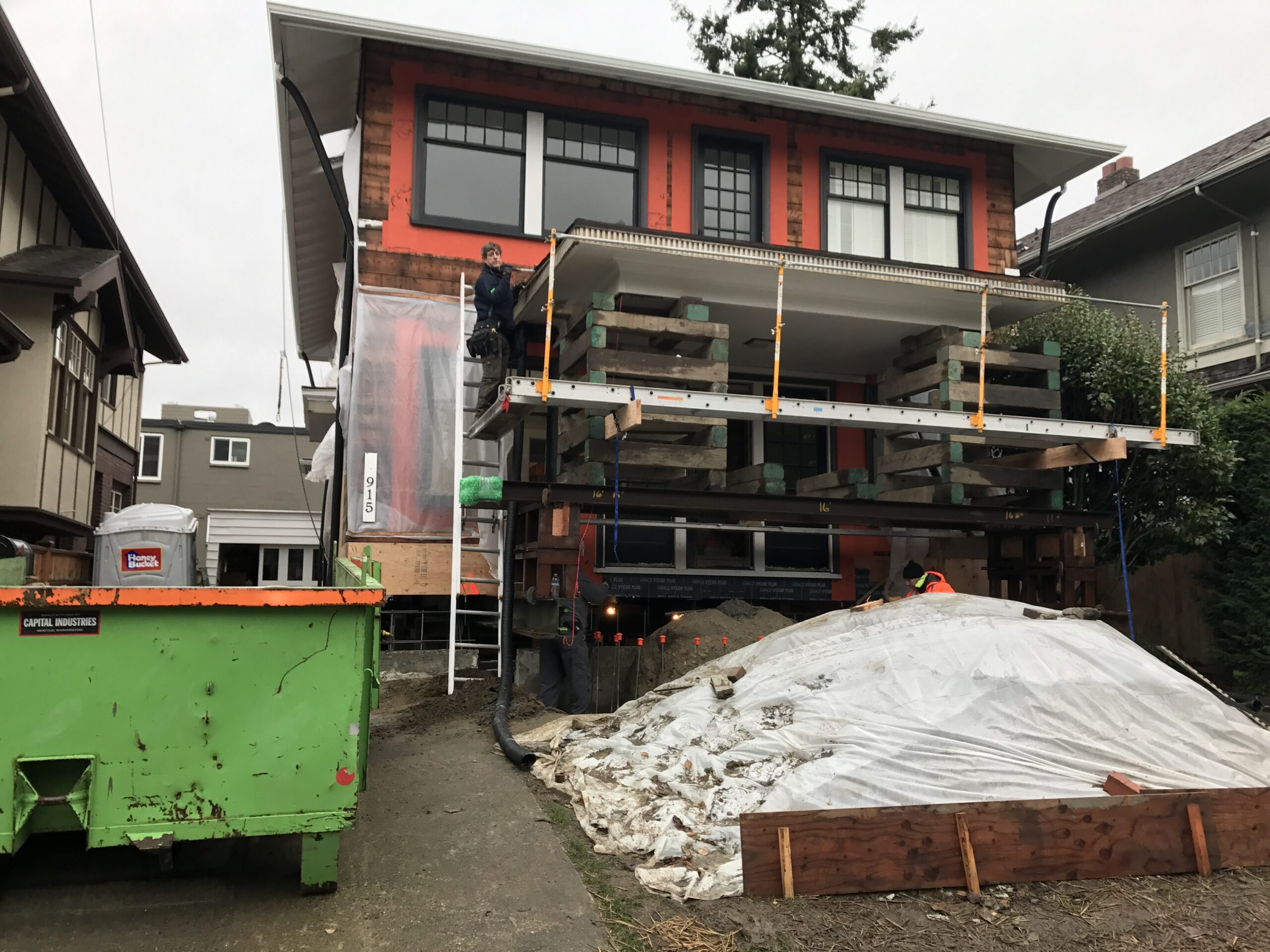
Here we the vapor permeable house wrap with new window sill covers and new window preprainted casing applied on the second floor windows. the entry roof is getting replacement dentils applied.
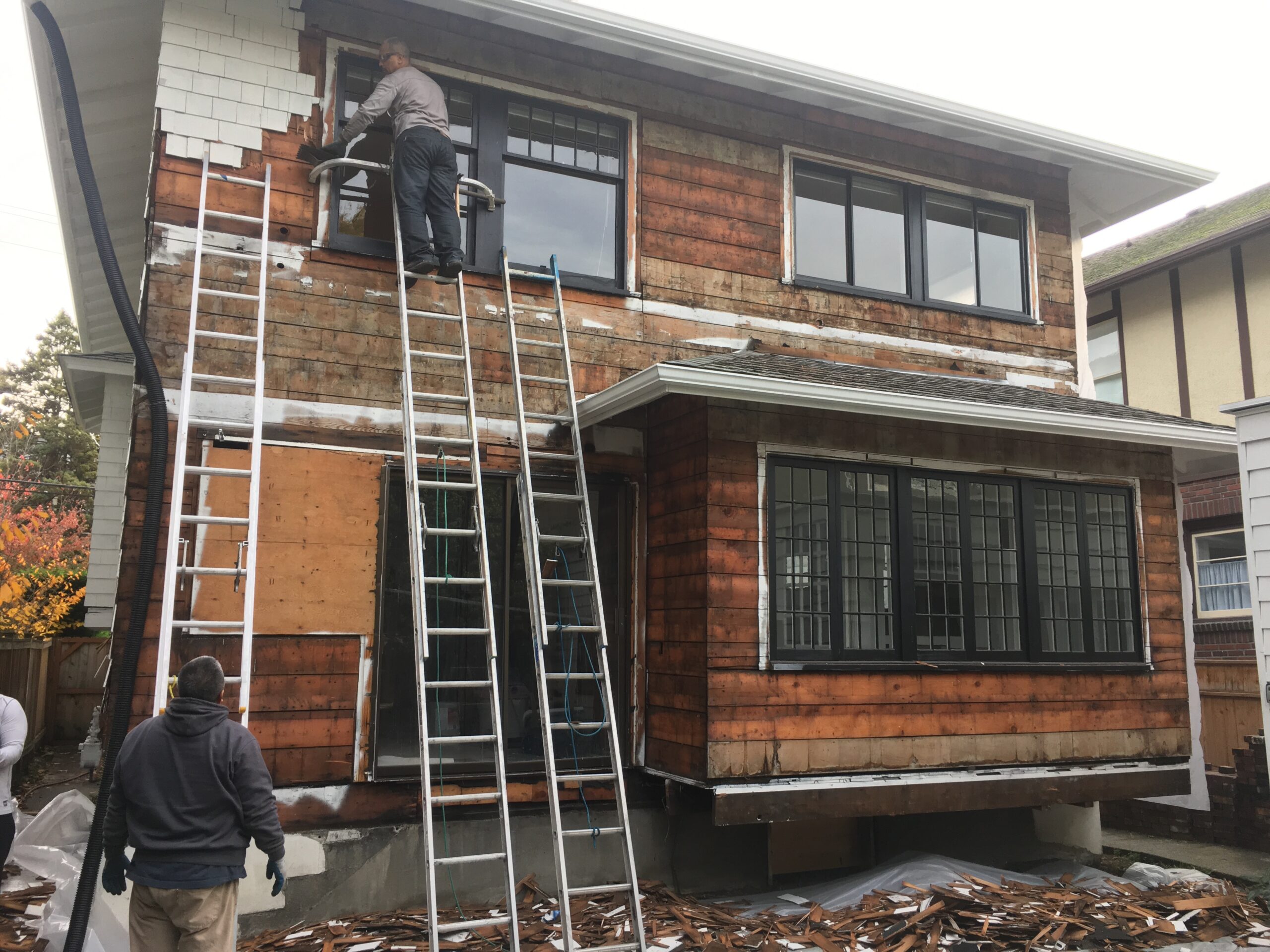
The test salvage of the old shingles did not pass. Here we see part of the process of removal of the siding.
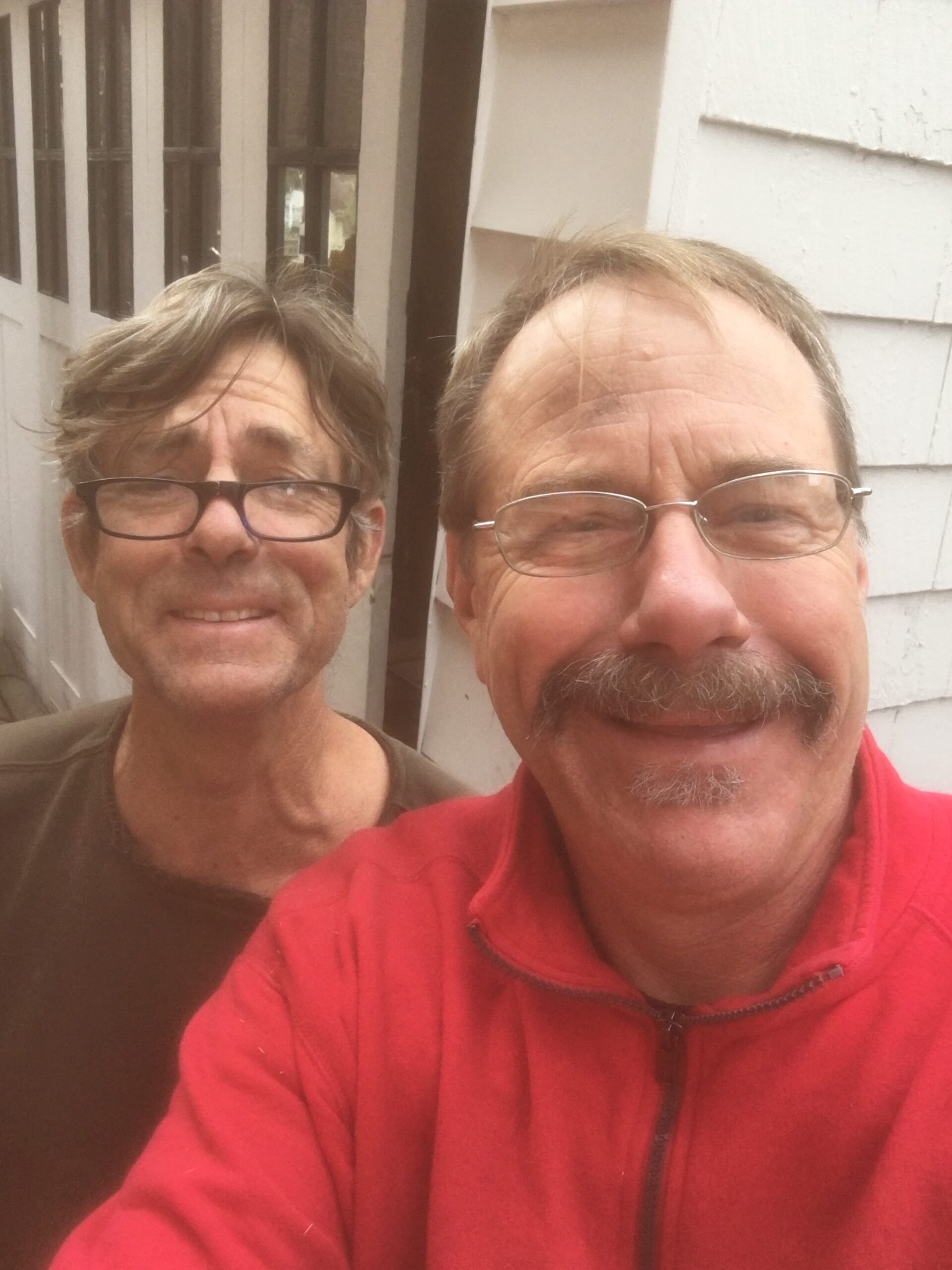
Part of the excellent crew on a very complicated project, Thanks Craig Baldwin!
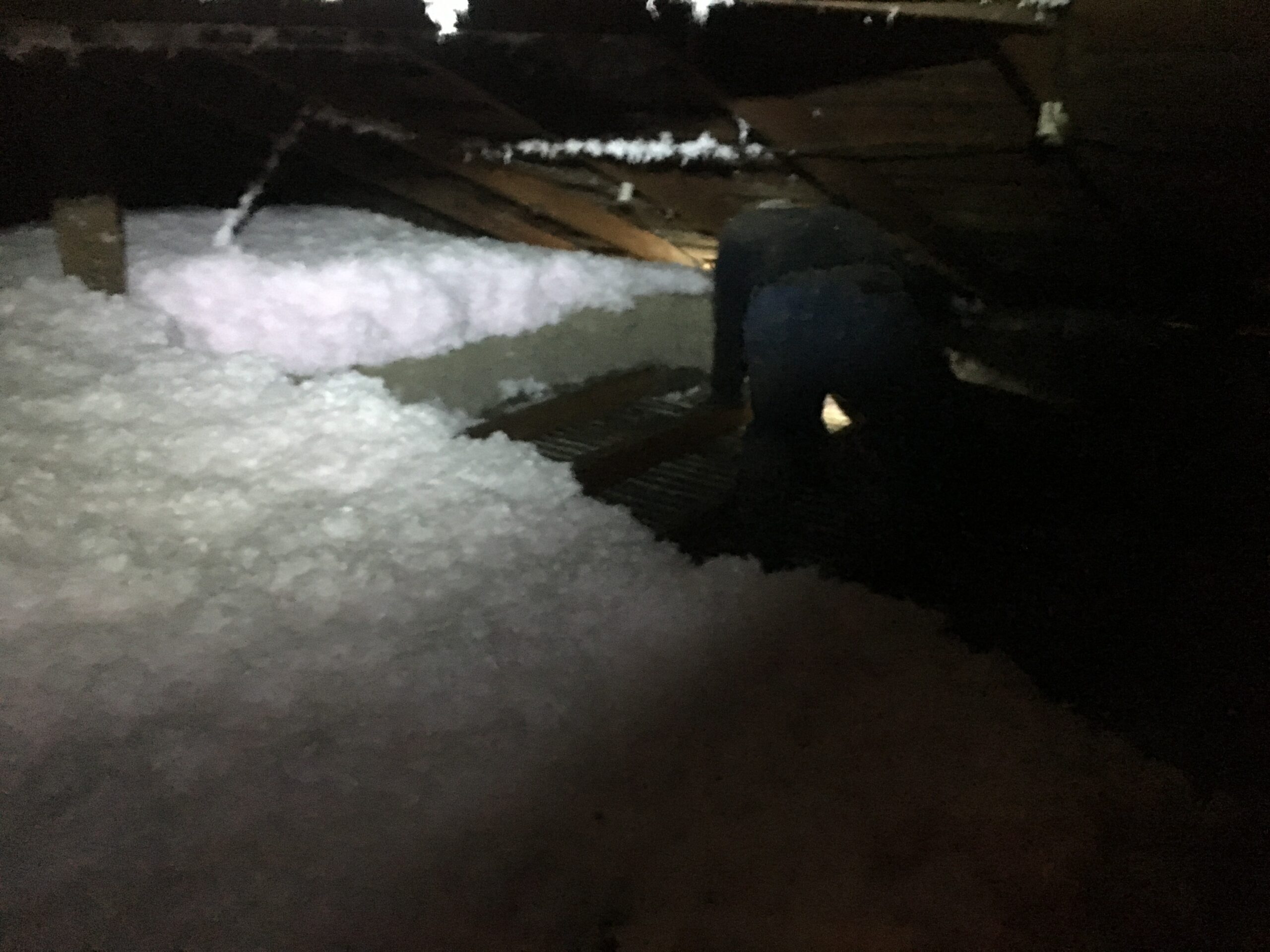
Early on 16 inches of blown in insulation was vacuumed out
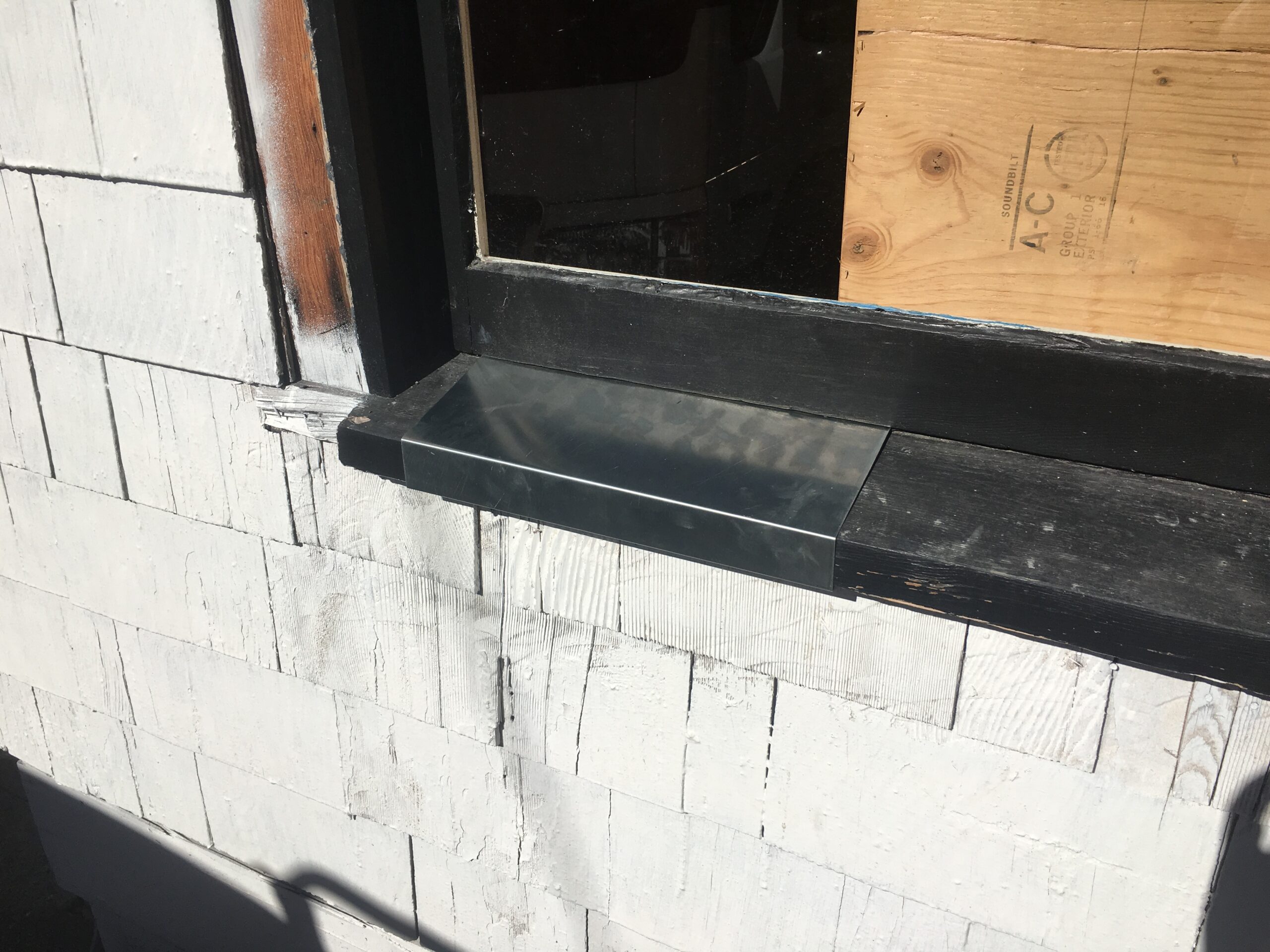
Test fitting window sill covers
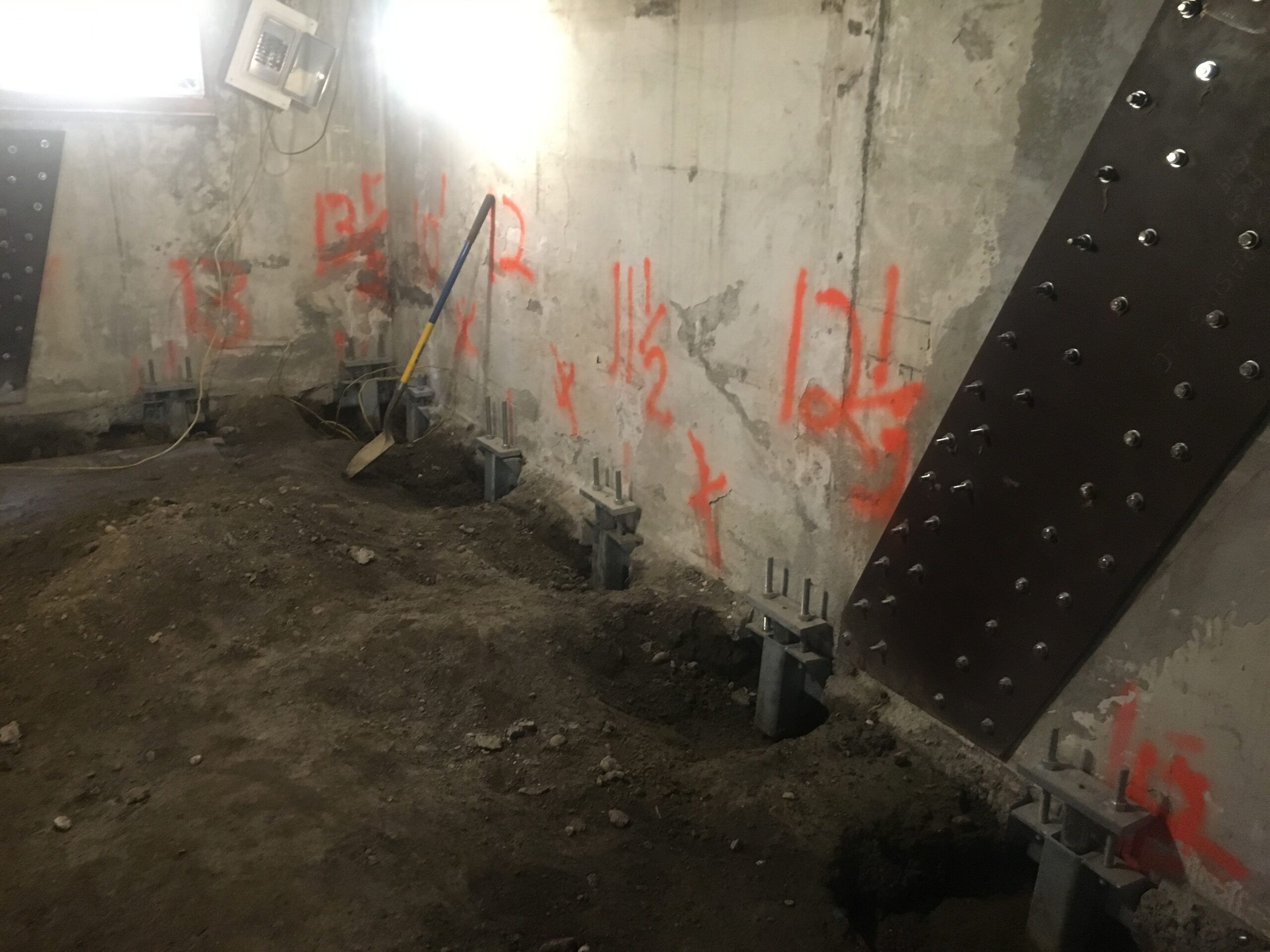
72 pin pile driven refusal, showing some of the under footing brackets. On the wall , 1/2 in steel plate bolted across cracks in the foundation walls
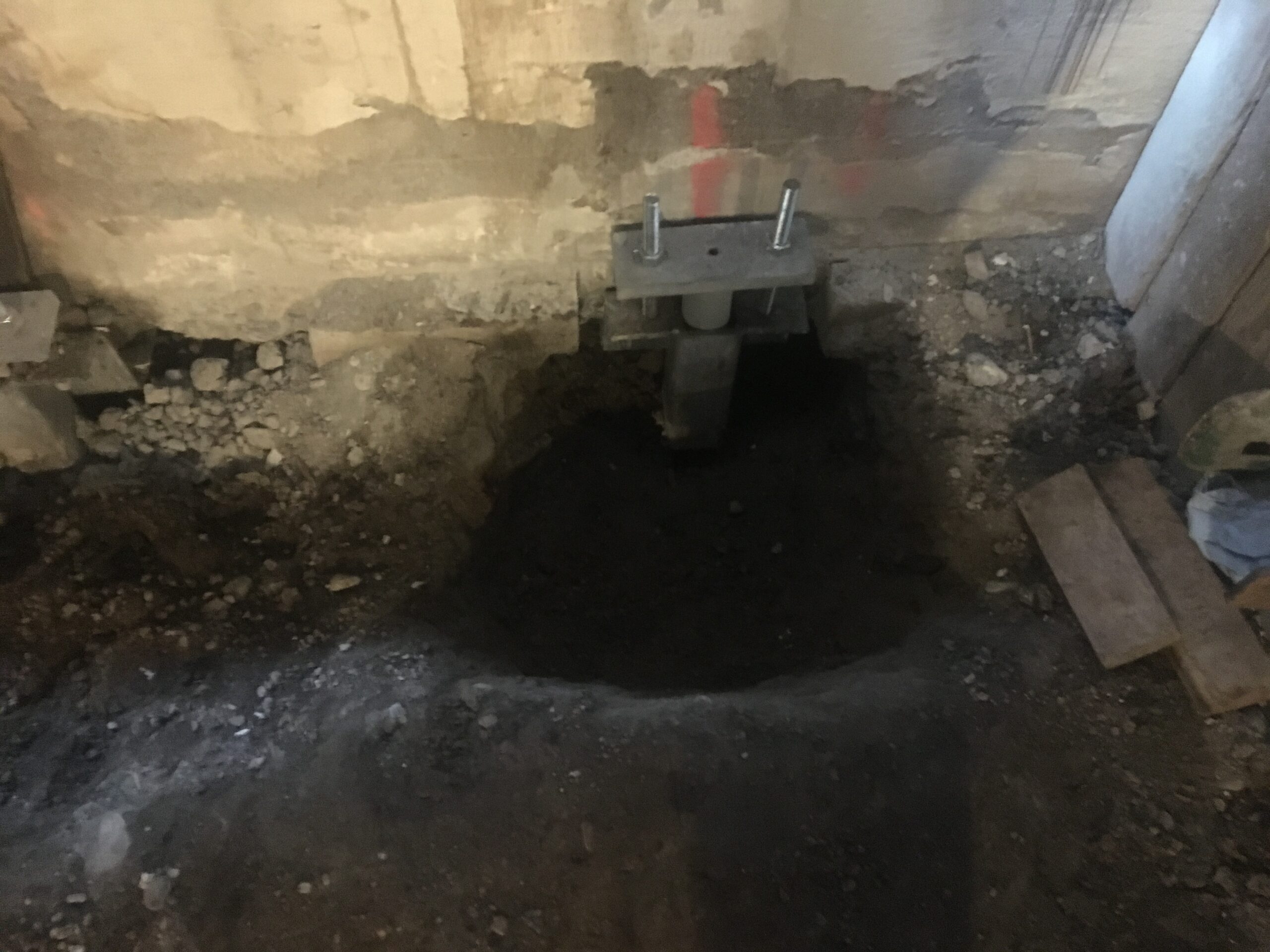
under footing Pin pile head
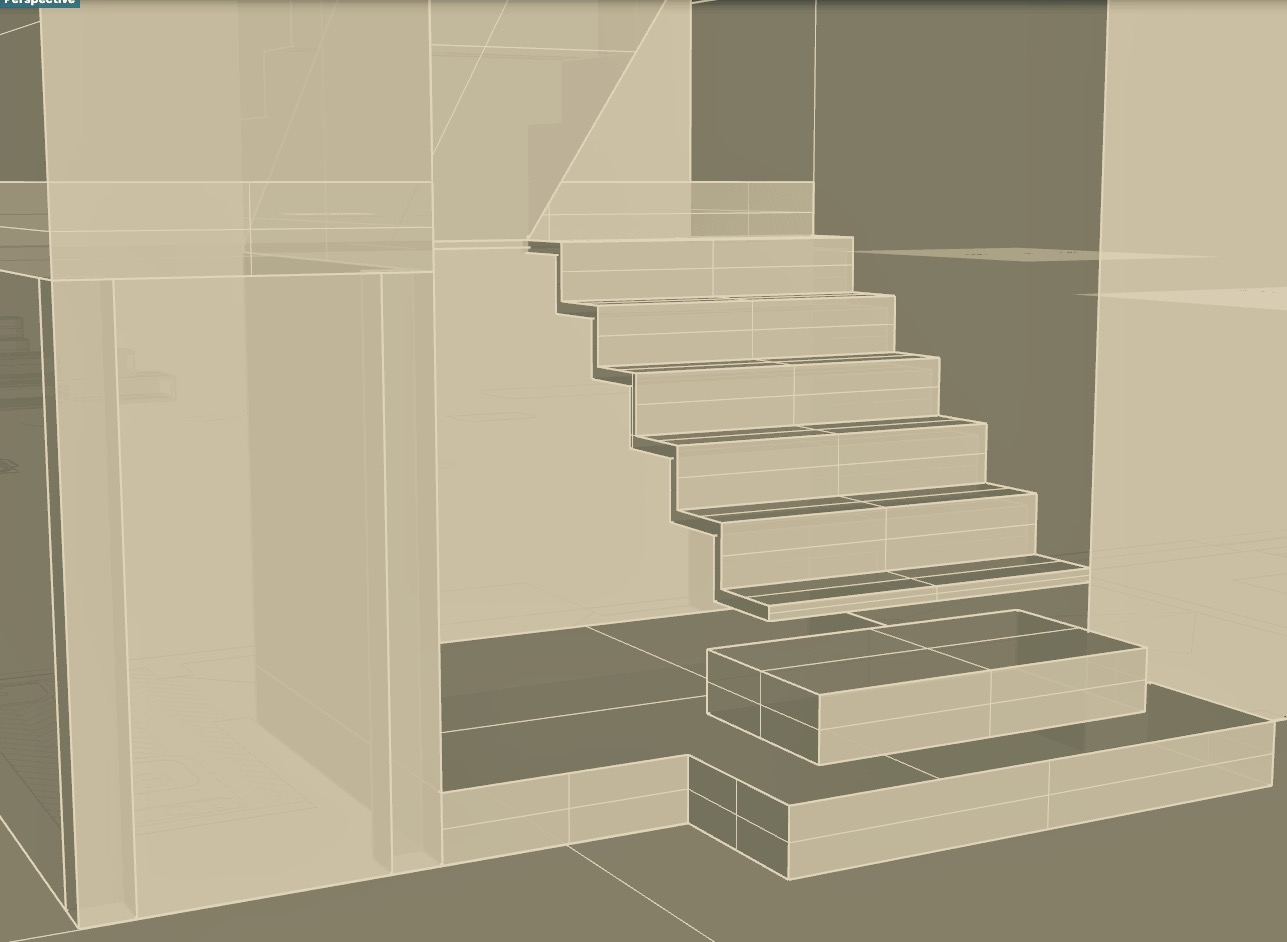
REndering of future floating basement stairs
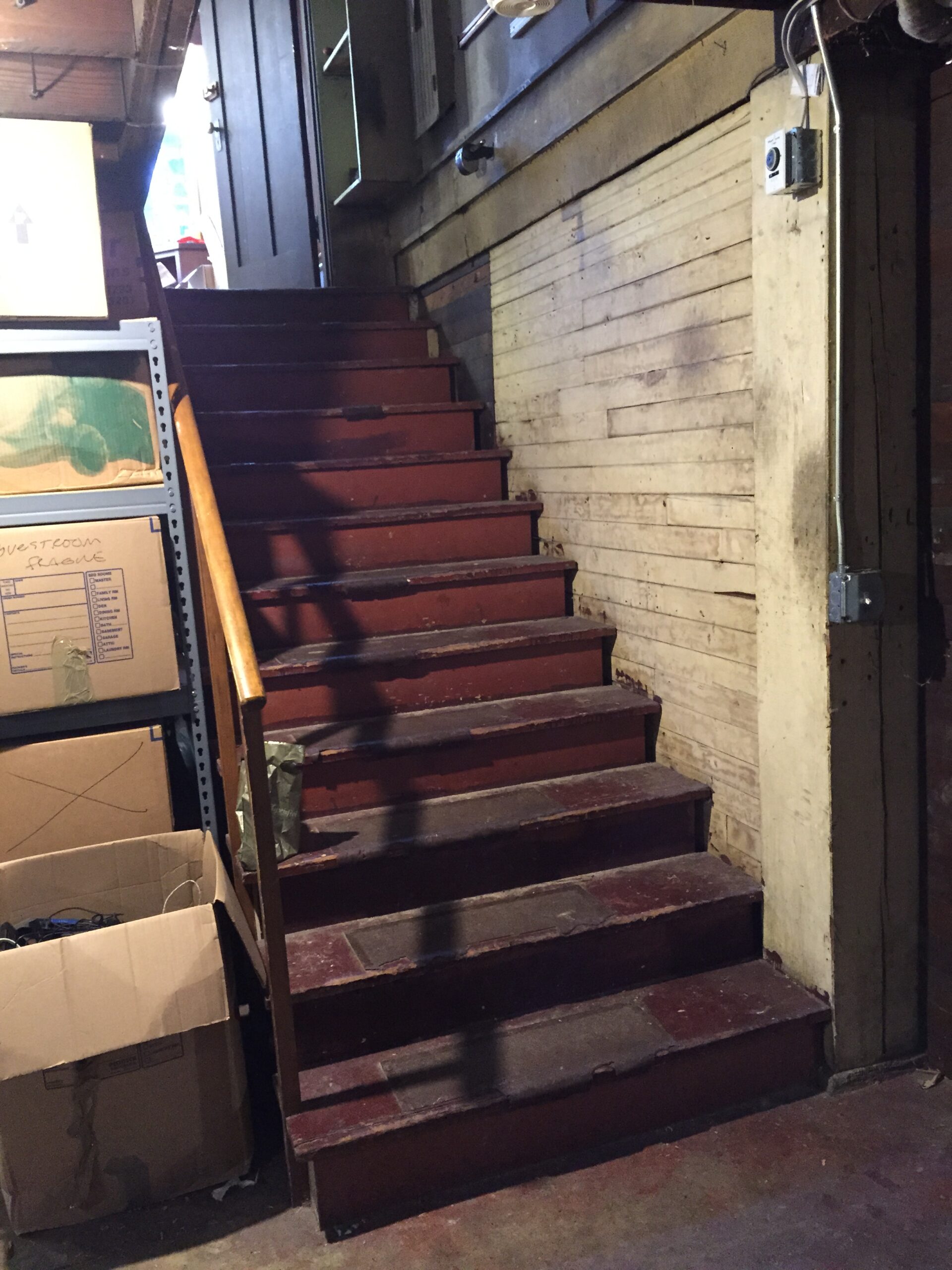
Old basement stairs before house lift
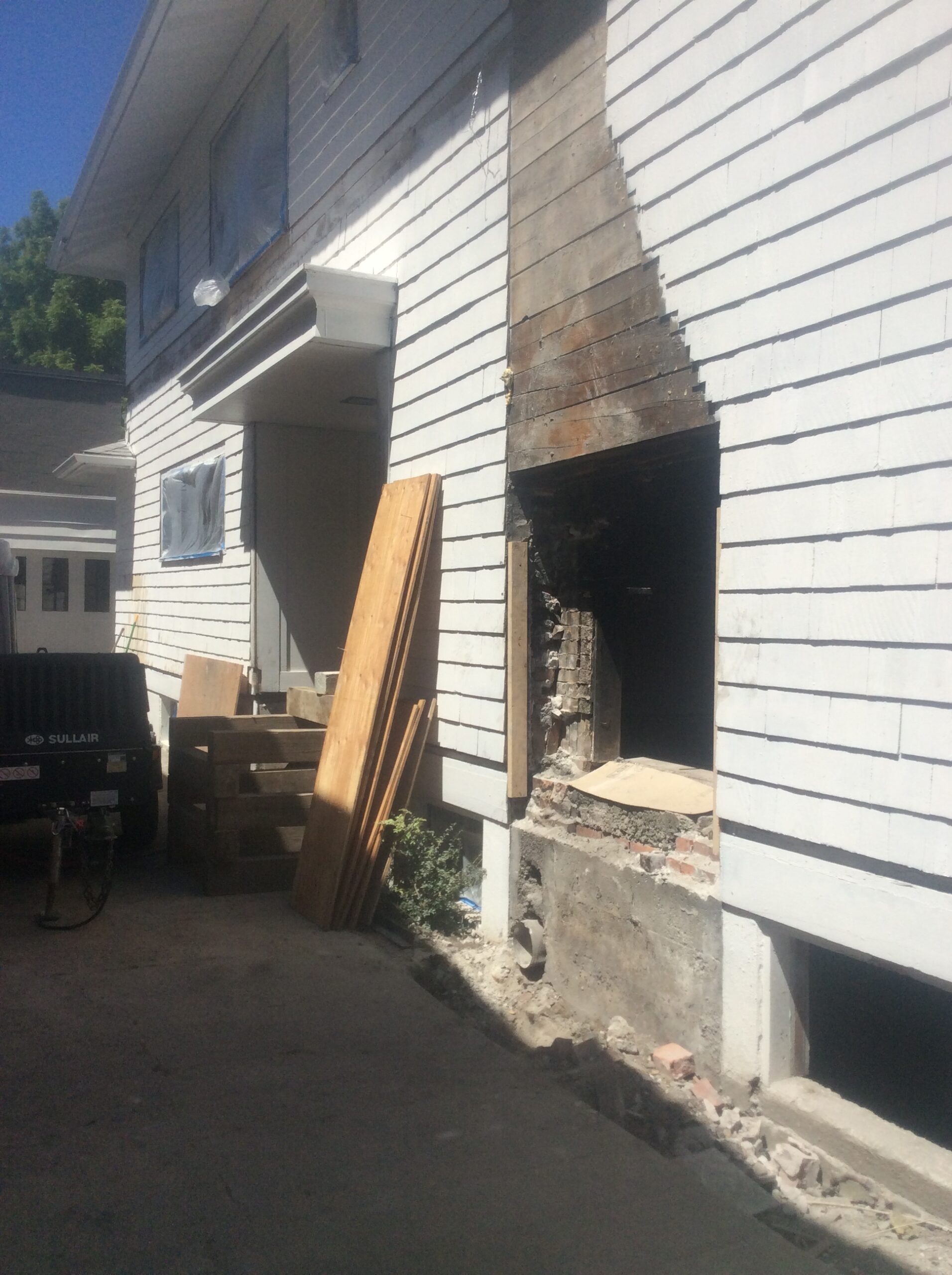
Since the building was to raised an assessment of the fireplace showed it was not structurally sound, so it was removed.